On-time deliveries, lean handling processes and as much automation as possible: optimal yard logistics sounds fantastic in theory, but is often difficult to implement in practice. Only when the yard becomes a smart yard can the individual workflows interlock perfectly and form a well-functioning network. The result: satisfied logistics partners and a logistics yard with the best possible capacity utilization.
In our blog posts, we repeatedly emphasize how important transparent communication is for yard management and therefore also for its individual components. However, the various workflows, such as check-in, appointment scheduling or call-off to loading points, are not only based on holistic communication, but also on the other processes. The aim of a smart yard is therefore to use collaborative approaches to make workflows more flexible and transparent. The result is an optimally controllable process for shippers, carriers and truck drivers.
Benefits of Digital Workflows
Yard logistics consists of many different processes that together form a functioning system. Many of these, such as slot bookings or notifications, are not strictly speaking the responsibility of the shipper. Rather, they are dependent on the input of external partners. Without sufficient communication, this can lead to unpleasant surprises that disrupt the shipper's planning. This can be remedied by digitizing these workflows, which offers further advantages for all logistics partners in addition to transparent collaboration and has a positive effect on the entire supply chain:
Notifications
Companies increase the transparency of orders and deliveries through digital notifications from their suppliers and the associated time slots. This means that staff on the factory premises have important information such as delivery quantity, truck license plate number, etc. long before the truck arrives.
Appointment Scheduling
The use of digital appointment scheduling optimizes and digitalizes incoming and outgoing goods management as well as capacity and resource planning. The system manages and allocates slots dynamically on the basis of defined rules, priorities and certain framework factors, such as expected arrival times or cut-off times. Yard management is most effective when appointment scheduling is integrated.
Check-in and Check-out
Incoming and outgoing transports and goods flows are traditionally controlled by barriers and gatekeepers. Smart Yard Management supports this step, for example by automatically registering truck license plates via camera and allowing them to pass through the barriers. Time-consuming checks against paperwork are no longer necessary.
Loading Point Call-Off
Waiting trucks are automatically called to the loading point via SMS, app or large display (LED screen). This saves personnel costs and reduces language barriers and communication costs.
Door and Ramp Management
With active resource management and automated free and occupancy signals, loading companies increase the utilization of their loading points.
Communication with Drivers
All parties involved in the transport and yard process can communicate with each other in the event of any delays, react immediately and coordinate and adapt any resulting changes, e.g. in slot allocation, accordingly. A central communication platform brings all process participants together and makes the progress of messages traceable at a later date, e.g. with the help of a ticketing system.
Control Center with Yard Visualization
By tracking resources and visualizing them in real time, the control station is able to detect deviations even from a distance and intervene in the ongoing process to correct them (management by exception).
Integration and Interfaces
Interfaces between all processes and adjacent systems, such as the transport management system and warehouse management, enable consistently transparent processes and precise documentation. If the degree of automation is increased through the interaction of the systems and, if necessary, the integration of hardware components, process robustness and efficiency are also improved.
Interaction of software and hardware
In order for shippers, carriers and truck drivers to benefit from a smart yard, it is first necessary to create a foundation for the system. For example, contactless yard processes drastically speed up the entire process. However, this requires not only a qualified software solution, but also the appropriate hardware - in this example, self-service terminals. This enables drivers to carry out the entire yard process independently, from arrival to loading and retrieval to departure. Contactless yard logistics means that there are no points of interaction with the shipper's staff throughout the entire process (no gatekeepers, teams at the loading points, etc.). Employees only intervene in the workflow in exceptional cases. An interesting side effect: the contactless yard process also reduces the risk of accidents and infection with diseases on the factory premises, as drivers no longer have to leave their vehicles. At the same time, the shipper's employees can focus on other important tasks.
The Smart Yard in Practice Example
The aim of contactless yard management is to enable truck drivers to carry out the entire loading process on the factory premises independently. In practice, this works roughly as follows:
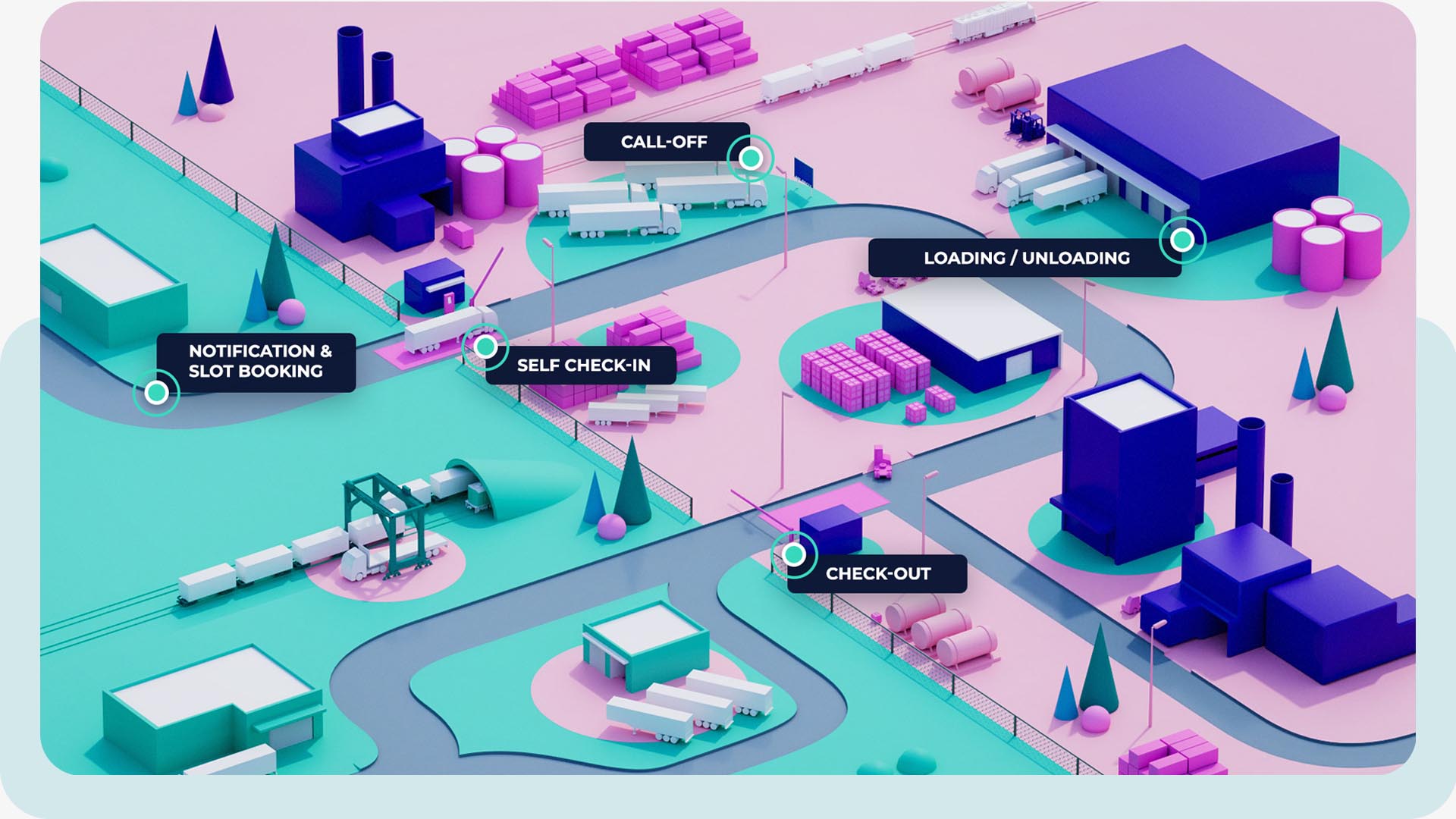
1. Notification and Slot Booking
First of all, the supplier must notify the delivery of a specific order and book a slot for his truck. Information such as the type of delivery, the recipient of the goods, the carrier, the registration number of the tractor unit and the trailer or even the country code are decisive for the shipper's planning. When the booking is made, a yard document is created in the background, whereby all the data from the booking is transferred. Depending on the order type, the parameters requested by the customer are then applied.
2. Self Check-in
When the truck reaches the factory premises, its first stop is the check-in. There, the terminal is already waiting for the arriving vehicle. If the device is aligned at truck operating height, the drivers can even remain seated in the vehicle for the registration process. A license plate camera captures the truck license plate from the front via infrared and recognizes the vehicle. If no camera is in use, users enter the relevant reference number to identify the order. The yard receipt is assigned in the background. The system plans and calculates the truck's onward journey. Another camera scans the rear of the vehicle and records the trailer's license plate number, which is important for the customs documents and is stored accordingly. Meanwhile, the truck is optionally placed on a scale that records the empty weight. At the end, the drivers may receive a printed loading ticket directly from a receipt printer in the terminal. This can contain further instructions, such as which waiting area to go to next.
3. Call-off
Once the vehicle has arrived at the parking lot, the drivers must wait to be called off. This is done automatically by the system as soon as a loading bay is free. In our example, this information comes in the form of a call-off on a large LED board that is clearly visible to all drivers in the parking lot. To make it clear which vehicle is allowed to drive onto which ramp, the display shows the loading ramp in conjunction with the corresponding license plate number of the truck.
4. Loading/Unloading
The process continues at the loading ramp: a scanner reads the previously generated loading ticket and the QR code on it. This provides the system with information such as the freight order number, ERP delivery, load quantity, etc. This step ensures that the truck is correctly located at the corresponding loading point and that a green light can be given for loading/unloading. After successful validation, the process begins.
5. Check-out
After successful loading, the truck moves to the check-out terminal. The set-up from the check-in is repeated here: The vehicle may be on a truck scale again, which now records the full weight. The terminal is at operating height, the drivers scan the ticket they received at check-in and start the check-out process. All data is sent to the connected ERP or transport management system via an interface. This is where the data is processed and the CMR consignment note is created. These legally required freight documents are printed out using the network printer integrated in the terminal (A4 thermal paper printer) and the drivers can pick up the documents without having to wait.
The Smart Yard also Works Without Hardware
With a Smart Yard, yard logistics almost runs by itself. By connecting the various partners - shippers, carriers and truck drivers - everyone is kept up to date. This offers the shipper in particular great advantages for planning their processes. For example, they are informed of delays at an early stage and can redistribute otherwise wasted resources to other workflows. This also makes space management in the warehouse much easier. At the same time, employees only have to worry about the truck drivers to a limited extent and are relieved of their tasks.