Handtmann Maschinenfabrik Achieves Transparency of Inbound, Outbound and Yard Processes in Just a Few Months
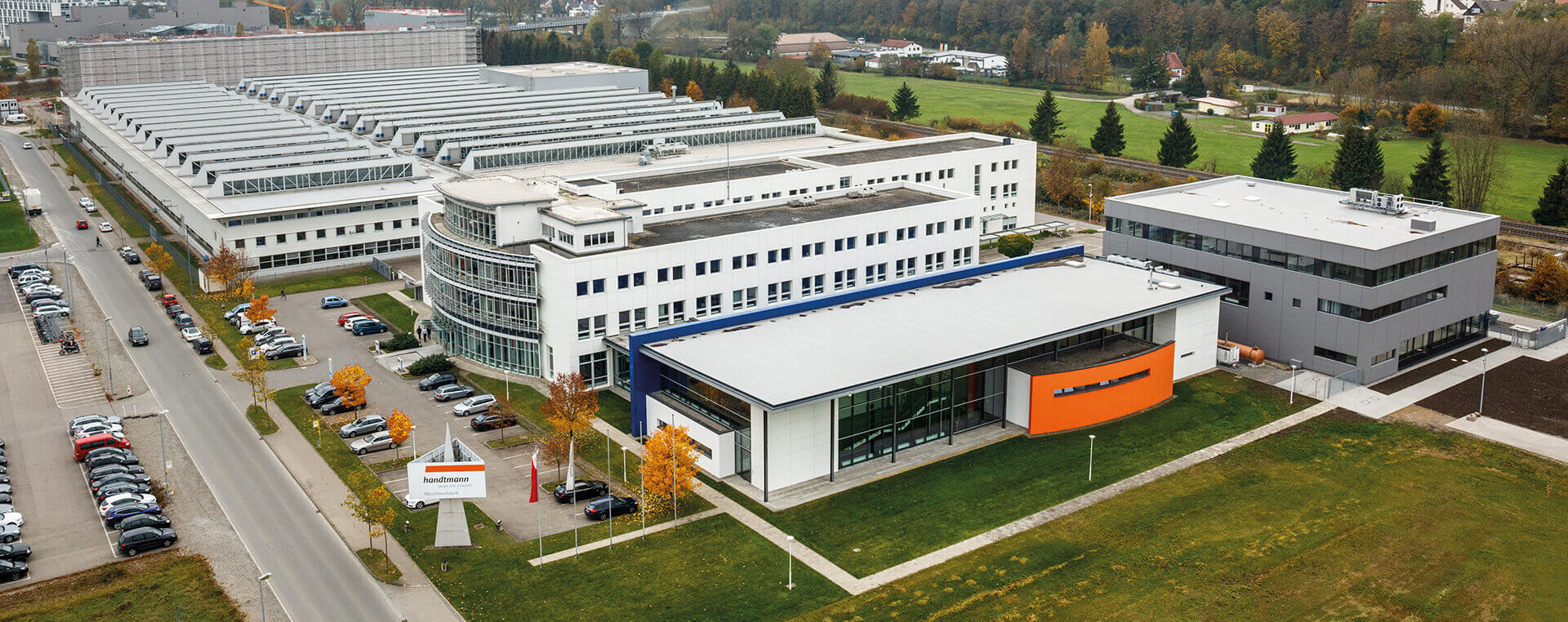
Industry: Mechanical Engineering
Employees: 1,500 (2023)
Annual Revenue: 374 M Euros (2023)
Locations: Biberach, Reutlingen, Zittau (GER), Hluk (CZ)
As a global player and market leader, Handtmann Maschinenfabrik in Biberach-Warthausen produces filling and portioning systems for the food industry on a large scale. In order to cope with increased transport volumes, the Swabian family business was looking for an integrated yard management solution.
About Handtmann Handtmann Füll- und Portioniersysteme
Handtmann F&P is the result of pioneering spirit and inventiveness paired with Swabian down-to-earthness, cosmopolitanism and a consistent focus on customer needs. Since its foundation in 1954, Handtmann F&P has achieved a great deal and played a leading role in the development of technology in the areas of vacuum fillers and portioning systems for the food industry. Today, Handtmann F&P is an international group of companies that offers integrated process solutions from product preparation to filling, portioning and separating technology through to product handling. In addition to the administrative headquarters and production site in Biberach, the Group also has sites in Reutlingen, Zittau, Amersfort (NL) and Hluk (CZ).
Further information on the product portfolio and current innovation projects can be found at Filling and portioning systems (handtmann.de)
Initial Situation
As a global player and market leader, Handtmann Maschinenfabrik in Biberach-Warthausen produces filling and portioning systems for the food industry on a large scale. In order to cope with the increased transport volume associated with the growth of the machine factory, the Swabian family business was looking for a holistic solution to bring the previously uncontrolled deliveries and pick-ups by external partners into an organised, levelled and, above all, transparent structure.
Solution
With the aim of better coordinating material deliveries and collections of spare parts and machines and improving the information situation on the factory premises, Handtmann opted for myleo / dsc including hardware support. With the help of Dock & Yard Management, including appointment scheduling, the manufacturer is now integrating its suppliers and customers or their carriers as well as the CEP service providers on the logistics platform into its yard management processes. The yard list in particular provides a better overview of which vehicles are currently present.
Key features of the application are
- Slot booking by suppliers, customers and hauliers
- Driver self-check-in via smartphone and QR code scan
- Information for those working at the gates about truck arrival; partly via optical and acoustic signal
- Tablet solution for forklift truck drivers
- SMS call for truck drivers when they can enter the site
- Access control through camera-based licence plate/vehicle authorisation
- Documentation of load securing during machine dispatch via photo

Results
In around five months, Handtmann Maschinenfabrik has managed to bring more transparency to its yard logistics in Biberach. The planning of incoming and outgoing transports is now easier thanks to the process integration of suppliers and service providers. The biggest plus is the database created with the help of myleo / dsc. It is now possible to carry out continuous process optimisation based on facts.
Benefits gained through the introduction of myleo / dsc:
- Key figure basis for optimising processes
- Smoothing of door utilisation throughout the week
- Preparation of spare parts and machine collections possible, as references are known in advance
- Communication options created with external partners
- Better coordination and more mutual understanding between process participants
- Coordination of customer-specific deliveries possible, resulting in reduced clarification effort
Your ContactWant to find out more?
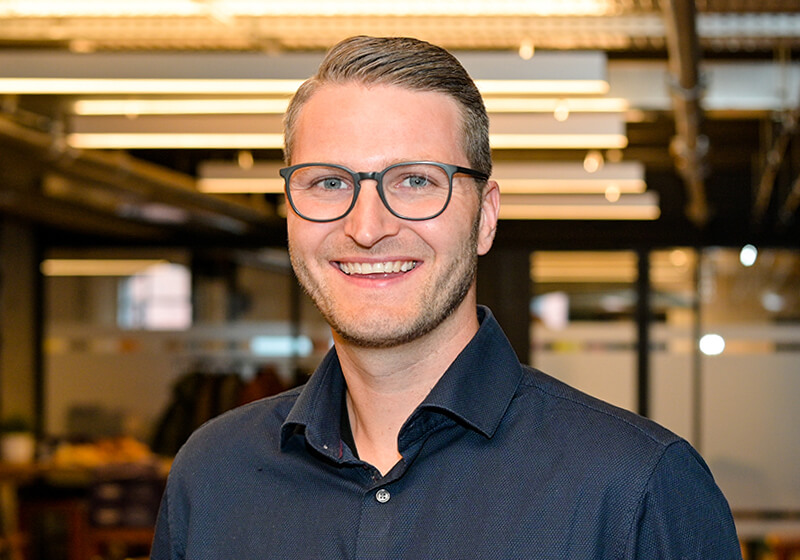
Vice President Customer ManagementMichael Rölli
Would you like to solve your logistics challenges in a simple, flexible and innovative way? We would be happy to support you in bringing your processes into the digital future. I look forward to hearing from you!