Nordzucker AG digitizes site logistics with myleo / dsc
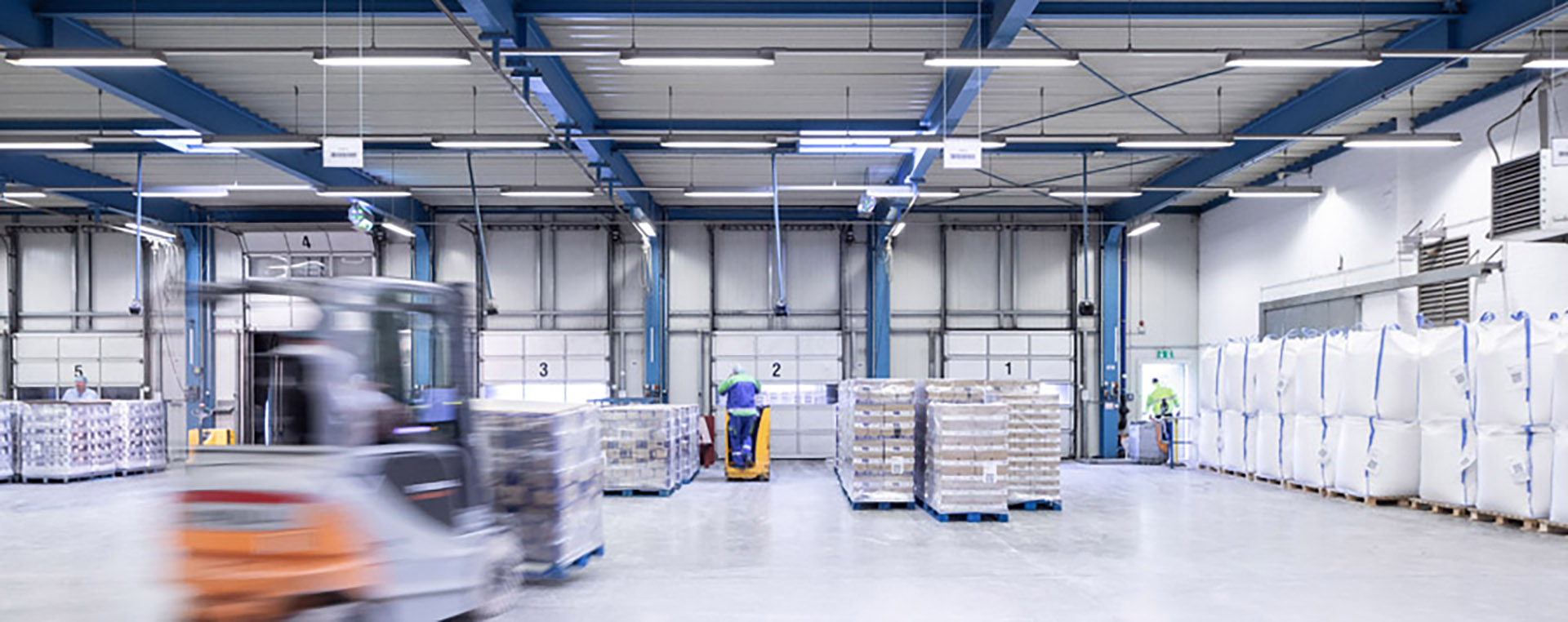
Industry:
Food
Number of employees:
About 3,800
Annual sales:
1.4 billion euros
21 production and refining sites in seven European countries and Australia, distribution sites in other countries
Without sugar, life would be half as sweet at best. To ensure that Nordzucker AG’s products arrive at supermarkets on time, the sugar manufacturer has converted its logistics to future technologies. Congestion and inefficiencies on the factory premises are now a thing of the past.
At peak times, bottlenecks frequently occurred on Nordzucker AG’s factory premises, depending on whether trucks were on time due to the traffic situation and whether supply from the warehouse could be ensured smoothly.
New system sought for transparent site logistics
Together with logistics solution provider leogistics, a state-of-the-art, cloud-based system has now been introduced that relies on the IoT (Internet of Things) and, thanks to geofences, knows an hour in advance which transport is on time. As a result, goods are automatically staged at the right ramp on time. In addition, a significant reduction in the length of the time slots for the trucks’ stay in the yard was achieved.
The company, which is headquartered in Braunschweig, also attached great importance to its vision of future-proof logistics planning. Accordingly, over the past few years Nordzucker has approached the digital transformation with a great deal of innovative spirit and a whole range of products from the leogistics portfolio in trusting cooperation.
The solution at a glance
- Yard Management: leogistics yard coordinates all activities of carriers and means of transport inside and outside the plant premises.
- Time slot management:Loading and unloading capacities are always kept in view and schedules are planned collaboratively with service providers and suppliers on a single platform.
- Track & Trace ensures transparency of processes and assets as well as **transport tracking in real time.**
- Trucks leave the yard significantly earlier since the introduction of automated retrieval processes.
- leogistics IoT: To automate the process of truck call-offs, Nordzucker relies on a currently prototypical sensor-based solution that is being implemented as a leogistics IoT scenario.
Comprehensive digitization with real-time data
It quickly became clear to the project team that real-time tracking of the trucks by means of track & trace was a “must-have” in order to be able to adjust time slots and provisioning from warehouse management accordingly in an agile manner. After the implementation of Warehouse Management SAP WM and leogistics Yard Management, the time slot management and the cloud solution myleo / tnt were implemented. A central component of Yard Management is the transport scheduling module Trans, which contributes to efficient planning by connecting all process participants involved. Only the overall combination enables maximum efficiency.
Integration is the magic word
Because a lot depends on the logistics partners, more responsibility was handed over to them in the new solution. Now they book time slots in a planning tool and reschedule them in case of problems themselves. In the beginning, drivers still proactively accessed a mobile app to manage their entire tour. In the meantime, on-board units and telematics solutions ensure automatic recording and transmission of the respective position. The myleo / tnt track & trace module, for example, follows the route of the trucks from start to finish.
When we chose leogistics, it was not just a matter of selecting a software supplier, but a strategic partner.
Michael Jansen, Head of SAP Standard Applikation Nordzucker AG
Higher loading efficiency thanks to complex calculations by myleo / dsc
If a truck is an hour’s drive away from the plant, exceeding the first isoline already triggers the retrieval in warehouse management from a high-bay racking. Triggering the retrieval process by myleo / tnt is based on a set of rules that only allows the process to start if a time slot for the estimated time of arrival has also been booked. The IDoc interface is used to trigger the high-bay racking which automatically removes the goods from storage onto the staging lanes, and to move the pallets to the loading gate.
Where it previously often took another hour after the arrival of the truck to prepare the goods, now everything is already on site when it arrives: That’s a considerable difference. With the introduction of the automatic retrieval processes, the truck leaves the yard much earlier and the time slot length has been significantly reduced.