Villeroy & Boch Achieves Transparency for Outgoing Transports

Industry: Bathroom furnishings
Employees: More than 6,000
Annual turnover: €995 million (2022)
Locations: 11 distribution centers in 8 countries
Villeroy & Boch was looking for an integrated platform to improve its planning and transportation processes. Today, myleo / dsc is used to identify bottlenecks at an early stage and communicate more transparently with partners.
About Villeroy & Boch
Villeroy & Boch is one of the world’s leading premium brands for ceramic products. Founded in 1748 and headquartered in Mettlach, the family-owned company stands for innovation, tradition and style. As a renowned lifestyle brand, Villeroy & Boch is represented in 125 countries with products in the Bathroom & Wellness and Dining & Lifestyle segments.
Initial situation
Villeroy & Boch was looking for an integrated platform to optimize its transport processes and increase planning efficiency. The previous tools did not provide sufficient transparency to meet the rising demands. It was particularly challenging to maintain an overview of all deliveries. The company needed a solution that enabled monitoring and proactive action to avoid bottlenecks.
Solution
For Villeroy & Boch, only a solution that enables automatic monitoring and notification of outgoing shipments was an option. This is why myleo / dsc with Dock & Yard Management including appointment scheduling, carrier commissioning and tracking & tracing is used. The company can now define precise time slots in collaboration with its carriers, track the transport status and optimize the processes in the yard.
The solution at a glance
- Central logistics platform for communication with partners
- Employees or freight forwarders book appointments and coordinate them jointly
- Dock & Yard Management enables efficient yard processing
- Digital check-in without additional hardware
- Fast CEP label printing through interfaces to CEP service providers
- Tracking & tracing provides an overview of transports
Results
Transparency in transport execution was increased, leading to improved delivery performance. The central platform enables transport activities to be coordinated efficiently, bottlenecks to be identified at an early stage and communication with carriers and suppliers to be optimized. Shipping labels for parcels are now also requested from CEP service providers via myleo / dsc and routed to the correct printer via the system integration with SAP ERP. Thanks to real-time monitoring and proactive alerts, transport delays are detected at an early stage.
- Replacement of many isolated solutions with central myleo / dsc platform
- Precise appointment scheduling for deliveries
- Avoidance of bottlenecks and delays
- Optimized processes in the yard and at loading ramps
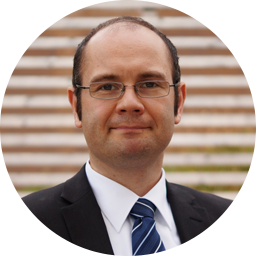
Your ContactWant to find out more?
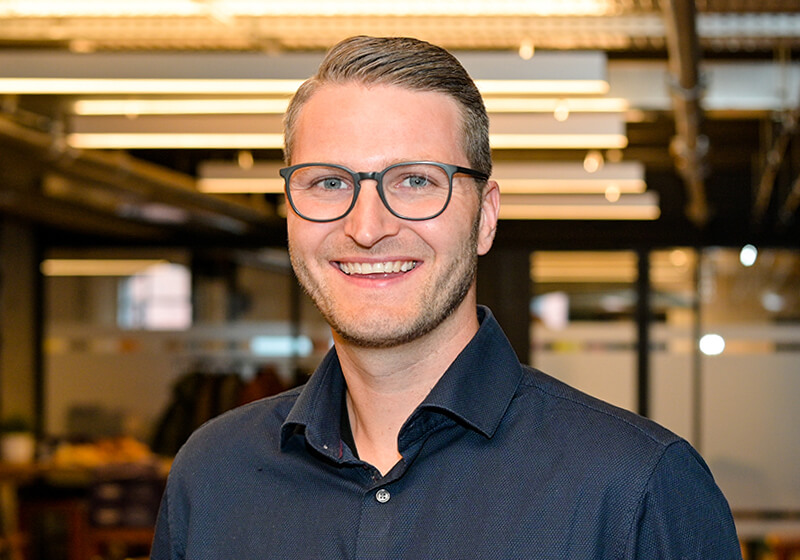
Vice President Customer ManagementMichael Rölli
Would you like to solve your logistics challenges in a simple, flexible and innovative way? We would be happy to support you in bringing your processes into the digital future. I look forward to hearing from you!