Max Bögl Optimizes Inbound and Construction Site Logistics
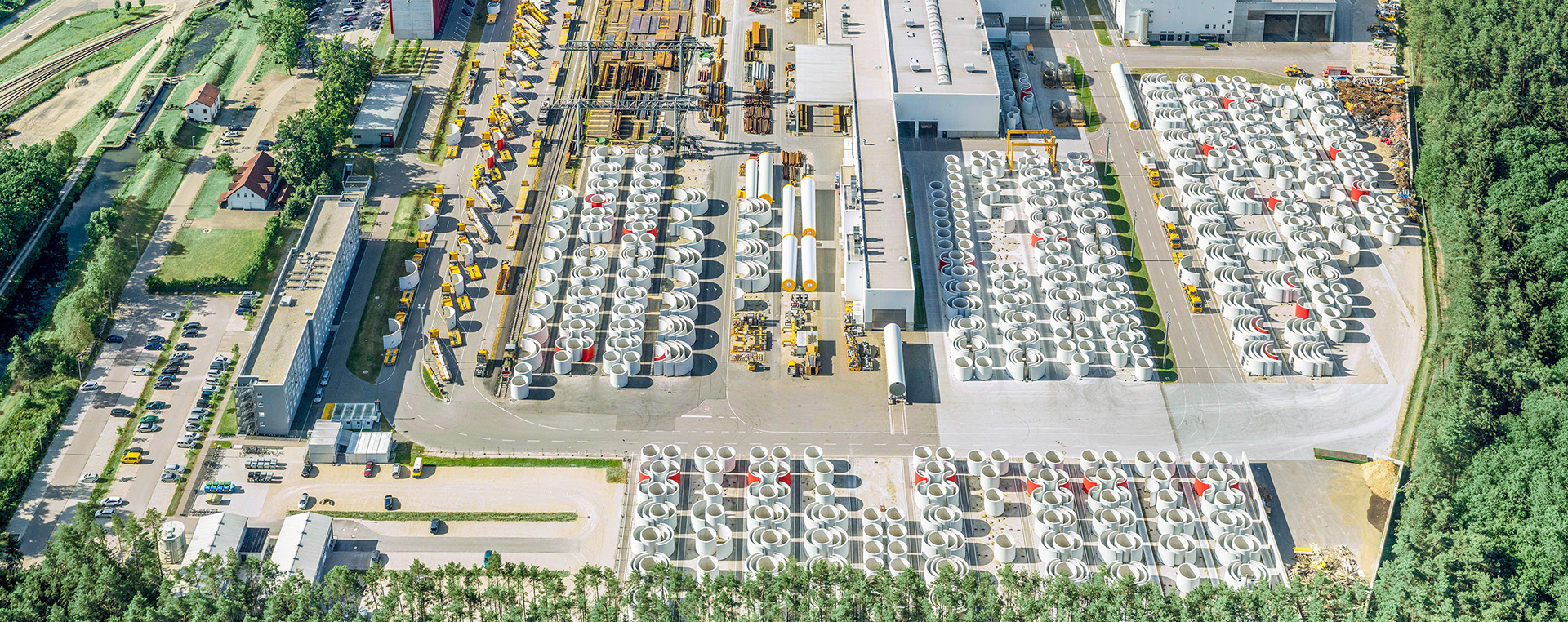
Industry: Construction
Employees: 6.500
Annual Revenue: approx. 2 billion euros (2020)
Subsidiaries: Sengenthal
The construction industry is under pressure everywhere: raw material and energy prices have risen dramatically, demands in terms of sustainability are becoming ever higher and regulations more complex. This is not the only reason why Max Bögl, one of Germany’s largest construction companies, needs smooth processes - not only on its construction sites worldwide, but also inbound at its Sengenthal site. For both, the company now relies on the myleo / dsc logistics platform.
About Max Bögl Wind AG
Max Bögl Wind AG is a subsidiary of the family-owned company Max Bögl, founded in 1929 and headquartered in Sengenthal near Neumarkt i. d. Opf. With around 6,500 employees, 40 locations worldwide and annual sales of over 2 billion euros, the group is one of Germany’s largest companies in the construction industry. The company’s range of services extends from building construction, civil engineering, bridge building, traffic route construction and steel construction to product development in the field of renewable energies.
Inbound optimization at Max Bögl Wind AG.
Greater efficiency in the inbound process includes, above all, an improved overview of time slots for loading and unloading and resource utilization on the plant site. For this reason, Max Bögl Wind AG at the Sengenthal site is now relying on the Supplier and Dock & Yard Management solutions of the myleo / dsc logistics platform. These include a delivery platform for coordination with suppliers, appointment scheduling and yard management. The aim of the implementation was to relieve the organizational burden on goods receipt. In addition, Max Bögl was concerned with transparency at its construction sites as to which prefabricated parts arrive when and in what quantity, in order to be able to implement projects faster and more efficiently.
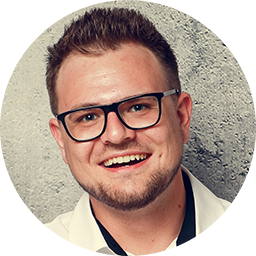
When Max Bögl receives an order, the order is planned by creating an SD (Sales & Distribution) order in the SAP system. As part of an MRP (Material Requirements Planning) run, the system compares the warehouse stock with the required order items. If goods are missing, a purchase requisition is created. Purchasing sends a purchase order to the relevant supplier as part of the master data. As soon as the supplier has confirmed the order, this is registered in the SAP system.
Digital notifications and slot bookings streamline deliveries
Since the implementation at Max Bögl, the orders from the SAP ERP are now transferred to myleo / dsc using an interface service and can be viewed here by the suppliers. They can now notify orders, including delivery quantities, within predefined opening and cut-off times and book time slots for them. In addition to the processing of slots by the Max Bögl team, it is also possible to divide an order into several time slots. The length is specified by the system depending on the specified order quantity and the pallets notified for it. In addition, it is mandatory for suppliers to provide each appointment with a reference number, the license plate number of the scheduled truck, and a contact person with telephone number to facilitate subsequent planning and processing.
WE REVOLUTIONIZE YOUR SUPPLY CHAINAre you ready to turbocharge your digital logistics?
High process reliability thanks to system-based mapping of yard processes
When the supplier’s truck arrives at the gate to the plant premises in Sengenthal, the delivery documents are first checked and, if necessary, the truck is weighed. Max Bögl now records the arrival with a time stamp directly in myleo / dsc. The truck then drives to the goods receiving office. Here, the papers and arrival time are compared with the previously notified appointment. During this process, Max Bögl can document all movements in the yard in the Yard Cockpit or in the yard list.
If the inspection is successful, the supplier can drive to the specified loading bay. There, the delivered goods are checked and unloaded. All steps are documented in myleo / dsc. Once unloading has been confirmed, the truck can quickly leave the factory premises again. The complete digital mapping of the inbound process not only guarantees a high level of process reliability, but also accelerates handling on the factory premises.
Max Bögl digitalizes construction sites with the help of myleo / dsc
Max Bögl also wants to optimize delivery processes on its construction sites. To this end, the construction company is relying on a simplified mapping of deliveries from internal suppliers, also with the help of myleo / dsc. This is expected to provide an improved overview of planned appoinments and resource utilization at the respective construction site. The decisive factor here is the delivery of finished parts in the guaranteed correct sequence, so that materials are only delivered and unloaded as soon as they are actually needed. The plan is for one truck per time slot to be traded for unloading and another in a waiting position.
In contrast to the use of myleo / dsc in Sengenthal, Max Bögl relies on stand-alone use of the logistics platform at its construction sites without a connection to an SAP system. Instead, the in-house truck dispatchers create advance notifications and time slots directly in the booking calendar of myleo / dsc, always providing information such as the precast part to be delivered, the quantity, and a part number. In addition, a QR code is attached. Restrictions on slot booking are imposed by opening hours, the selection of only one gate and a lead time of 48 hours, although for simplicity all time slots are 30 minutes long. The site team can shift the time slot if necessary.
When a truck arrives at a construction site, the arrival is confirmed by the construction site team using a mobile device in myleo / dsc. The delivery is then checked and unloading is also booked on the logistics platform. Once everything has been unloaded and documented in myleo / dsc, the truck can be on its way again. By planning with the help of the Process-as-a-Service platform, Max Bögl can handle the delivery processes in a more coordinated manner than before and use the limited space on the construction sites more efficiently.
Foto: Max Bögl Wind AG, Reinhard Mederer