Loading point utilization plays a critical role in yard logistics. Often, the arrival of trucks, swap bodies and trailers is not evenly distributed over the opening hours of the plant site. The occupancy of loading points is the key factor in the efficient organization and execution of logistical processes on the yard. Ideally, the timing of transport equipment at loading points is seamless. If this is not the case, myleo / dsc now offers a new functionality!
Trucks arrive and are directed to a parking lot, if the loading point determination does not find a free loading point for loading and unloading. This parking lot serves as a buffer location. In the Yard Cockpit, the loading point scheduling can track the current operating situation at the gates or ramps at any time. If all loading stations are occupied, the next means of transport is only called up when a loading station becomes free.
The departure of a means of transport can be reported manually, via a sensor or from within the process - for example, via a mobile application that confirms the end of the loading or unloading process. The retrieval of the next means of transport according to the ranking is done as a push message to the driver, via a large screen display or similar.
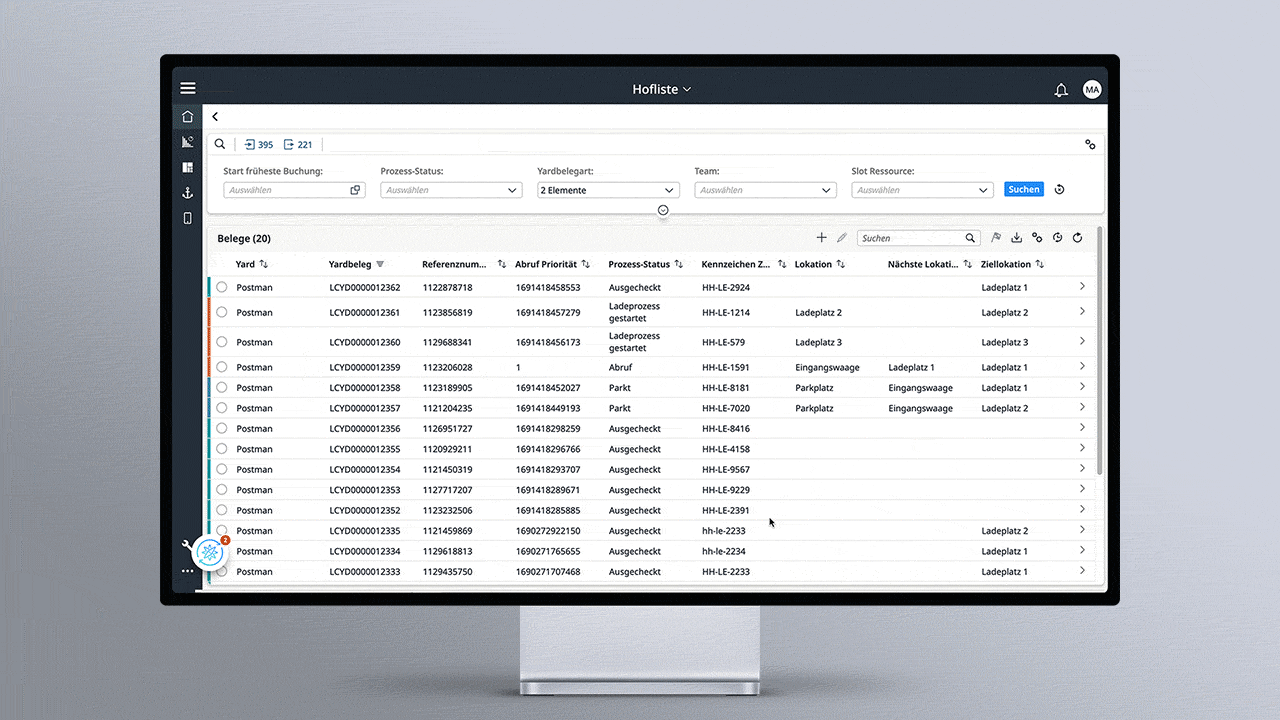
Manage Loading Point Call-Offs More Precisely
For the initial sequence determination, a ranking is created. This can be influenced by individually definable criteria. Of course, the ranking can only include all factors to a limited extent, and there are exceptional situations in which a different decision must be made beyond the initially calculated ranking. For these situations myleo / dsc now offers new possibilities:
1. You can override the ranking with a higher priority of a loading process and thus achieve your prioritized processing.
2. You can select an alternative loading place and thus achieve a faster processing.
In some situations, a combination of both options can also lead to success: To do this, simply select an alternative loading point while increasing the priority.
Improved On-Time Delivery Thanks to Efficient Loading Point Control
By improving and facilitating loading point management in this way, you achieve greater resource efficiency and also save costs, for example by improving productivity in terms of loading capacity, forklifts and labor.
The bottom line is that you can also have a positive effect on your delivery reliability and customer satisfaction: a well-organized loading point capacity utilization makes it possible to process orders on time. After all, if the truck is already late at the site, it can never arrive at the customer's on time. More efficient loading point management thus makes it possible to meet delivery deadlines, which in turn increases customer satisfaction and strengthens long-term customer relationships.
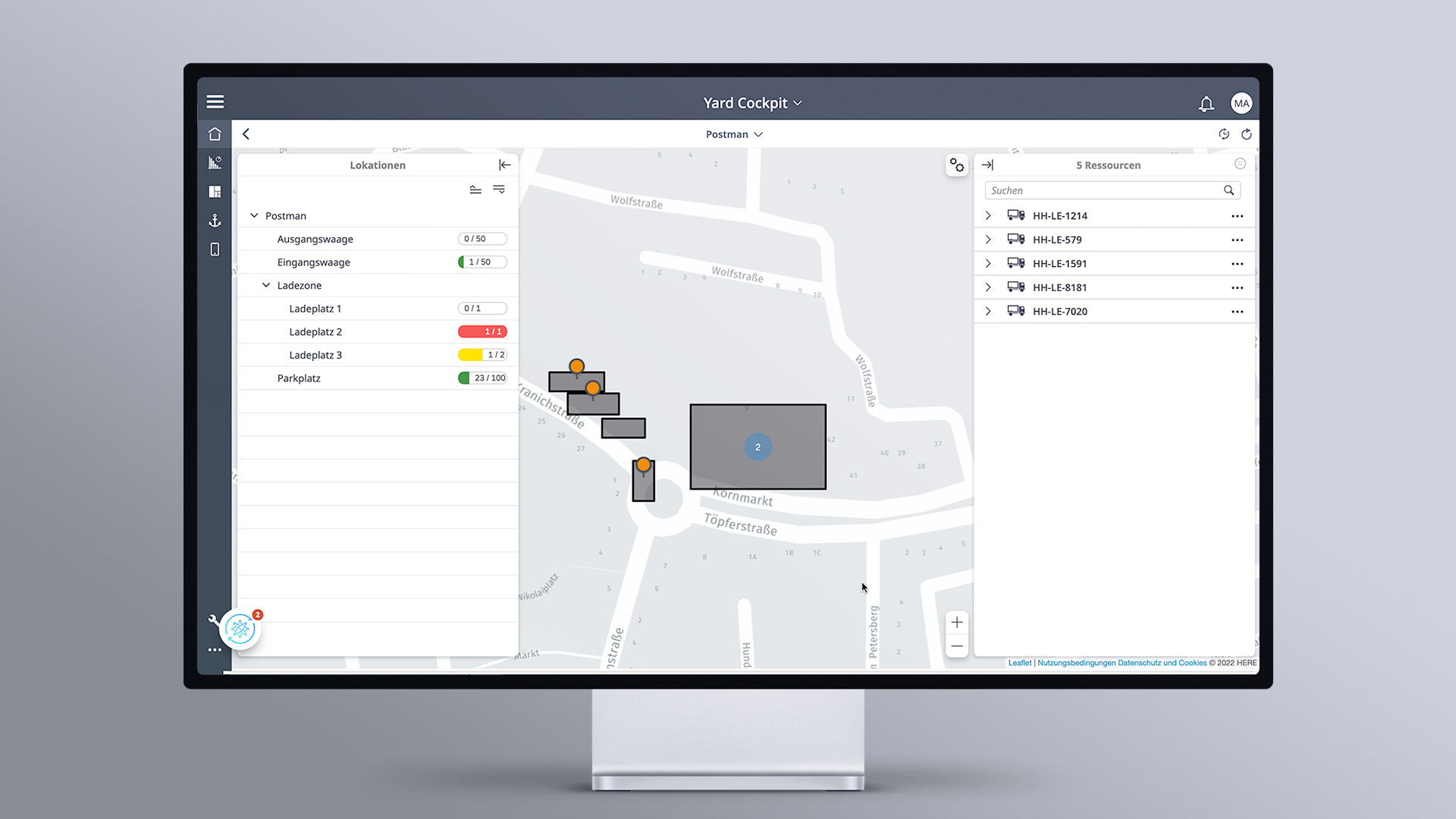
Better Planning Creates Safety and Control over Material Flows
More balanced loading point utilization can also contribute to yard safety. Overcrowded or chaotic loading points can lead to accidents. Clear organization and utilization can minimize such risks.
Finally, accurate monitoring of loading point utilization also makes it possible to track the flow of materials, identify bottlenecks at an early stage, and better plan production. As a result, delivery delays can be avoided and the entire logistics structure can be improved. myleo / dsc supports you here with a wide range of functions.