Procurement logistics is one of the most important disciplines in the entire supply chain. It is responsible for ensuring that the necessary materials or goods reach production or the incoming warehouse. Depending on the organization, this can present a variety of challenges for suppliers or shippers. Specialized software solutions provide the necessary support for the diverse procurement strategy.
Procurement Logistics at a Glance
The transport of goods is at the heart of procurement. To ensure that this runs smoothly and the goods can reach the recipient without any problems, the supplier must transmit a range of information. This includes general attributes of the delivery such as weight, size or type, but also planned delivery periods. Depending on the commercial clause or Incoterm (see info box), there is also additional work for the shipper. For example, in the case of an EXW (Ex Works) delivery term, the shipper bears full responsibility for the goods as soon as they have been packed, marked and made available at a predefined location by the supplier. This means that the buyer is also responsible for transportation and related costs. Conversely, in a DAP (Delivered At Place) clause, the seller is responsible for the means of transport and transportation.
Errors in transport planning can accordingly have far-reaching consequences for suppliers, shippers as well as consignees and, depending on the delivery conditions, mean breaches of contract. It is therefore in the best interest of the partners to optimize procurement and to make all related information available in a transparent manner. But this is easier said than done, because the effort involved in recording and transmitting information appears huge at first glance - especially if the processes are manual. This creates challenges that are detrimental to procurement and distribution logistics and make life difficult for the recipient of the goods.
The Five Biggest Pain Points in Procurement Logistics
The biggest hurdles in procurement logistics usually start with inbound delivery management, but only become apparent much later, e.g., during gate management. The result are avoidable problems that also affect the further course of the supply chain:
1. Goods arrive unsecured in front of the premises
If the shipper does not receive any information about the delivery time, it can occur that a truck unexpectedly drives up at the gate. If no free storage space is then available, the supplier or carrier has to wait. Although it reads as if this primarily affects the supplier, it quickly becomes the shipper's problem. It is not uncommon for drivers to suffer from time pressure and decide to unload the goods themselves at the entrance to the yard. This is particularly questionable in the case of fresh deliveries and hazardous goods transports and can also lead to theft of the goods.
2. Chaos in warehousing
If the transporter is standing in front of the gate or the goods land in front of the logistics area without being requested, it is in the best interest of the buyer to transport them to the warehouse as quickly as possible. This becomes problematic as soon as all storage bins have already been allocated. Because then the subsequent deliveries lose their reserved space - so the problem is not solved, but postponed until there is no more space available for staging.
3. Production planning suffers
All elements of the supply chain are closely linked and delays affect every subsequent process. In production logistics, it is therefore critical to know and plan ahead for the timing of material delivery. If the goods receiving department does not know this time, it cannot allocate personnel or resources, nor can it plan warehousing. As a result, the company runs the risk of production coming to a standstill due to stagnant supplies. An absolute no-go, because this entails immense costs.
4. No goods receipt
If the shipper does not want to take a risk because of lack of storage space and critical goods information, they can also refuse an unexpected delivery. In this case, the supplier harms themselves: Because they not only have to bear the costs for the return, but also possibly risk the business relationship with the carrier and shipper due to the delay in delivery.
5. Sources of error fall under the radar after goods receipt
Without the necessary information, there is also no way to trace goods deliveries that have already been made. If the goods are damaged or incomplete, for example, there is no clear documentation under these circumstances. Consequently, the shipper bears the loss because he accepted the goods from the supplier in good conscience. In production logistics, a more far-reaching problem also arises: important materials are missing and have to be reordered first - the supply comes to a standstill. The shipper thus loses valuable time and possibly even customers due to the supply bottleneck.
In addition to the major pain points caused by missing information, there are other challenges in procurement logistics. These include language barriers, dissatisfied employees or customers, and undocumented delays, for example due to traffic accidents. Complex site traffic can pose a risk to the safety of delivery drivers during the registration process at the terminal. Many of the hurdles that arise can usually be overcome through transparent communication between all parties. A digital solution can also overcome language barriers or ensure error-free documentation of goods information.
Solution: Procurement Logistics with myleo / dsc
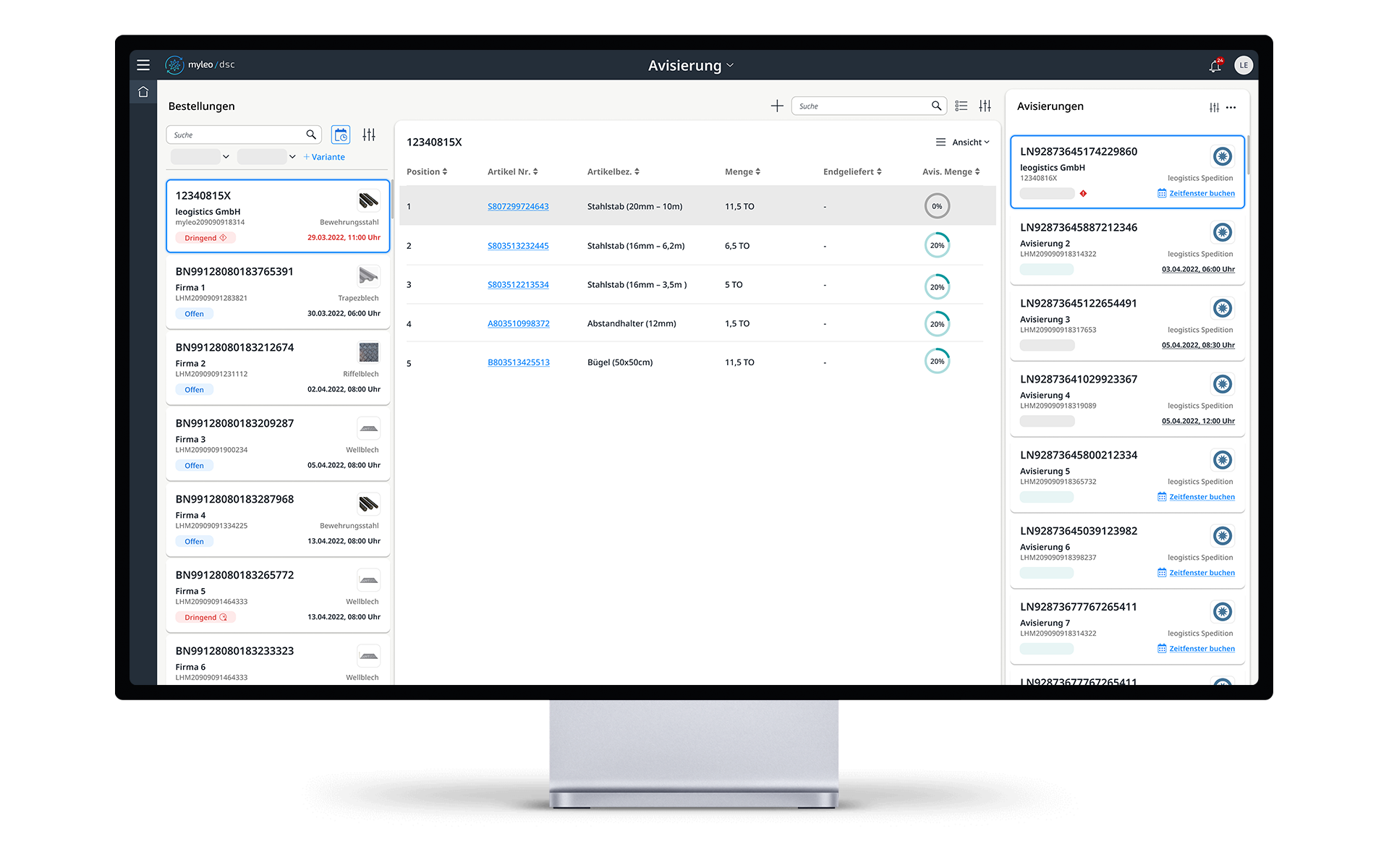
As a platform for Dock & Yard Management, among other things, myleo / dsc offers many useful features for managing all important yard processes. In addition to flexible appointment scheduling, automated capacity calculations and communication options for logistics partners, the solution also provides a loading bay call-off function. This means that waiting trucks are automatically called to the respective loading point via SMS, app or large display after they have registered at the self-check-in and a suitable loading point becomes available. The terminal provided for check-in is designed at truck operating height so that drivers can control the process from their trucks and are not exposed to the sometimes dangerous site traffic.
myleo / dsc also supports digital notifications including associated delivery time slots, which significantly increases transparency throughout the entire process. This renders unannounced deliveries and undocumented process information a thing of the past. Together with the terminals or web applications, which can be easily accessed via smartphone and support many different languages, goods or timing information can thus be transmitted and viewed even at short notice.
With the help of digitization and transparent flows of goods, the right information is available in the right quality at the right workplace: All parties involved in procurement logistics are efficiently connected with each other. The consequence is reduced costs, better control of processes, and even possible growth for the company.